Проблемы внедрения бережливого производства (Lean Production)
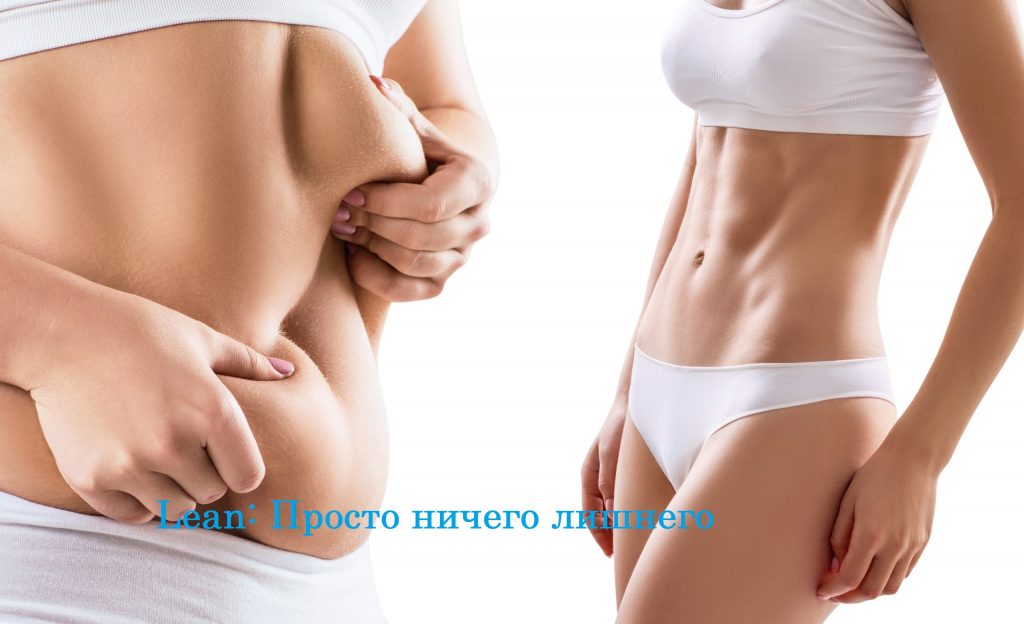
Принято считать, что проблемы внедрения бережливого производства (Lean production) в других странах возникают в основном из-за отличий менталитета японцев от менталитетов других народов
Да, менталитеты европейских и азиатских народов отличаются. И это может вызывать некоторые проблемы при внедрении Бережливого производства (Lean Production), но эти проблемы вполне решаемые. Если европейцы в процессе познания идут от сложного к простому (от большого к малому), то восточные народы – от простого к сложному (от малого к большому). Российский же менталитет отличается и от западного и от восточного. Мы всегда пытаемся идти от сути (центра) в обе стороны одновременно – в сторону простого и в сторону сложного. Мы сразу стараемся уловить главный смысл, а потом уже на досуге думать, что, как и почему. И это, конечно, самый лучший (самый эффективный) способ познания. Сначала создается логический «скелет» в виде строгих закономерностей, который потом постепенно обрастает подробностями как мясом. Но, как только мы уловили суть, нам становятся неинтересными дальнейшие рассуждения. Мол, зачем о чем-то рассуждать, если и так уже все понятно. Поэтому наше превосходное умение моментально схватывать суть предмета имеет и обратную, нехорошую сторону. В народе это объясняют выражением «верхушек нахватался». Человек много о чем имеет представления, и верные представления, но он совершено не знает тонкостей, деталей, не является знатоком, профессионалом, не в состоянии эти представления применять на практике. Есть и еще один неприятный момент в реализации нашего сознания. Пока нам не удается построить в голове строгий логический «скелет» какой-то теории (уловить суть), мы будем годами и даже десятилетиями это обсуждать и спорить, даже не задумываясь о внедрении в практику. Я уже приводил в пример SWOT-анализ (SWOT-анализ – оценка уровня конкурентоспособности), разработанный миллион лет назад, примерно в то же время что и бережливое производство, но так и не нашедший еще практического применения в нашем бизнесе. Японцы, например, внедрили его сразу по ознакомлении, и любая, самая мелкая, компания использует его в каждодневной практике.
Под разговоры об особенностях японского менталитета всегда как-то упускается из виду, что бережливое производство придумал американец Уильям Эдвардс Деминг, который, собственно, их и обучал этому на протяжении многих лет. Далеко не сразу они смогли все это усвоить, но зато когда усвоили, то уже не могли работать по-другому, и на протяжении десятилетий постоянно совершенствовали эту систему.
В Америке мало кто знает, кто такой Деминг, хотя именно ему мир обязан созданием системы бережливого производства. Когда Деминг создал свою систему (цикл Деминга, смертельные болезни массового производства, принципы управления, план внедрения принципов управления) и пытался ее популяризировать в Америке, то она не встретила горячего одобрения со стороны бизнеса. Уж очень она противоречила привычному укладу производства. Бизнес просто не видел смысла ее внедрять, в 50-х годах прошлого века у американского бизнеса все было хорошо, так зачем было что-то менять. Зато японцы, которые после войны страстно желали перестроить свою недоразвитую промышленность, с удовольствием прислушивались к советам Деминга. Зерно упало на благодатную почву. У нас говорят – нет пророка в своем отечестве, а оказывается, как у Высоцкого, «да и в других отечествах не густо».
Уже на протяжении десятилетий в США среди американских компаний разыгрывается приз за самое полное внедрение бережливого производства. Каждый год американцы определяют победителя, но еще ни разу японцы не признали, что хоть одной американской компании удалось внедрить у себя бережливое производство. О другом мире можно даже и не говорить. Считается, что если американцы, со своей развитой промышленностью и высокой культурой производства, не в состоянии это сделать, то что уж говорить о менее развитых в промышленном отношении странах. Хотя, это очевидная глупость. Сама Япония является свидетельством того, что внедрение бережливого производства не зависит от высокого уровня развития промышленности. Как, кстати, и от наличия или отсутствия американского менталитета
Содержание:
Основная причина неправильного понимания системы бережливого производства
Базовый принцип бережливого производства
Принцип вытягивания
Принцип создания «потока»
Принцип постоянного совершенствования Кайдзен
Принцип «Обеспечения качества с первого раза»
Принцип принятия решения «Немаваси»
Принцип визуального контроля процесса Канбан
Принцип «поставка точно в срок»
Пресловутые 6 сигм
Основная причина неправильного понимания системы
бережливого производства
Мир заинтересовался бережливым производством только тогда, когда Япония уже вышла в мировые промышленные лидеры. Тогда американцы заинтересовались, а как это ей удалось. По уровню промышленного развития она не только догнала, но во многих областях обогнала США и европейские страны. Ярким примером такого превосходства стала компания Тойота. Когда американцы решили понять, чем вызван успех Тойоты, и обратились к японским промышленникам с вопросами, японцы были очень удивлены. Они делали только то, чему их учил Деминг и ничего другого. Им и в голову не приходило, что американцы могут не знать систему Деминга, зачем же они спрашивают о том, чему сами их учили. А американцы удивлялись, причем тут какой-то Деминг. Им казалось, что японцы просто хитрят и не хотят открывать свои секреты. Американцы упросили позволить им самим посмотреть, как устроено производство Тойоты, чтобы самим разгадать тщательно скрываемые секреты. Японцы охотно им это разрешили. Представляю, как они удивлялись – что за странные люди, сами нас всему научили, а теперь подозревают нас в том, что мы что-то от них скрываем.
Когда американские специалисты стали на месте анализировать систему производства, они не могли ее понять. Стали задавать японцам вопросы, на что они очень подробно отвечали. Но японцы отвечали на японском языке. И в этом суть проблемы. Японский язык очень скуден, поэтому, чтобы выразить мысль, которая на английском языке предается одним предложением, на японском языке она может быть выражена только несколькими предложениями. Получалось, что на один простой конкретный вопрос японцы отвечали несколькими предложениями. Это выглядело так, что на вопрос они отвечают какой-то притчей, призванной что-то скрыть. Американцы сердились, опять задавали вопросы, а японцы опять отвечали «притчами». При этом, японцы постоянно ссылались на Деминга. Это злило американцев еще больше, опять какие-то отговорки. Когда до японцев дошло, что американцев особенно злят ссылки на Деминга, они просто не в курсе кто это, и какая там у него была система, они перестали на него ссылаться. Американцы обрадовались, ну вот, перестали хитрить, а то несли какую-то ахинею. В результате, японцы объяснили американцам все свои принципы организации производства, т.е. принципы Деминга, но уже в японской интерпретации и в переводе с японского. Американцы все тщательно записали и начали строчить книги о японском чуде и о японской системе бережливого производства.
Все знания о бережливом производстве, которые нам сегодня доступны из литературы, это грубый английский перевод японского осмысления принципов Деминга. Перевод потому и грубый, что американцы переводили, не особо вникая в тонкости. Чем экзотичнее сведения, тем больший интерес они могут вызвать у читателя, тем лучше будут продаваться книги. А после этого весь остальной мир был уже обречен тиражировать эти американские исследования.
Есть еще, конечно, и японская литература, переведенная на английский язык. Она, понятно, не ограничивается только опытом компании Тойота и ее принципами, все японские копании исповедуют бережливое производство. И эта литература дает очень точное объяснение принципов бережливого производства, но подается это, конечно, в японском стиле, в виде притч или изречений, которые необходимо дополнительно осмысливать. Достаточно трудно построить из набора этих притч строгую логическую схему.
Если иметь неправильное или просто туманное представление о какой-то системе, то трудно надеяться на ее внедрение, и тем более на ее эффективность. Такое внедрение всегда будет лишь имитацией внедрения. Чтобы показать, почему бережливое производство не поддается внедрению, достаточно привести несколько примеров неверного понимания его основных принципов
Базовый принцип бережливого производства
Под разговоры об японском чуде был фактически похоронен (замылен) базовый, самый главный принцип Деминга, гласящий, что целью деятельности любой компании является постоянное совершенствование качества ее товаров или услуг. Это трудно понять и принять сразу, но это именно так. Прибыль не является целью деятельности компании. Получение прибыли – это цель собственников компании. А компания – это механизм, машина обмена ценности, предоставляемой компанией своим покупателям, на прибыль. В Японии есть свое особое определение прибыли. Это не разница между доходами и расходами, а часть той ценности, которую компания предоставляет своим клиентам, которой клиенты готовы с компанией поделиться. Чем большую ценность компания приносит своим клиентам, тем большей ее частью клиент готов поделиться с компанией, и тем большую прибыль она приносит своим собственникам. Поэтому, постоянное улучшение качества своих товаров и услуг (увеличение предоставляемой клиентам ценности) – это цель деятельности любой компании. Нет необходимости отдельно думать о прибыли, она автоматически рождается из увеличения ценности, предоставляемой клиентам. И, наоборот, чем больше сегодня компания экономит на качестве (гонится за сиюминутной выгодой), тем меньшую прибыль она будет приносить в будущем. Это прямая и железобетонная зависимость, хоть и растянутая во времени.
Из этого принципа, как из семени, произрастают все другие принципы бережливого производства. Если исключить этот принцип, то система бережливого производства сразу превращается в прах. Этот принцип – и есть основа той «волшебной» философии, которой руководствуются японцы, и которую категорически отказываются понимать американцы и прочие европейцы. На практике американцы пытаются к своему так называемому «массовому производству» привязать на веревочку инструменты бережливого производства или, еще смешнее, переделать эти инструменты («усовершенствовать») и уже эти суррогаты применить. Инструменты бережливого производства бессмысленно пытаться пришить к массовому производству, это лишь имитация борьбы за эффективность, но американцы (и не только они) с упорством, достойным лучшего применения, пытаются это проделывать снова и снова. Именно поэтому японцы еще ни разу не признали ни одну американскую компанию (которая выигрывала в конкурсе США по определению лидера по внедрению бережливого производства), действительно внедрившей бережливое производство
Принцип организации вытягивания
Принцип организации «вытягивания» на самом деле это не один принцип, а два:
– создание потребительского (внешнего) вытягивания,
– создание внутренней цепочки связей Заказчик-Поставщик.
Если с созданием внутренней цепочки «Заказчик-поставщик» все довольно ясно (хоть и очень непросто на практике), то создание потребительского вытягивания просто игнорируется. А без внешнего вытягивания невозможно построить внутреннего вытягивания. Имитировать, конечно, можно, только какой в этом смысл.
Если создание внутренней цепочки связей – это, суть, вменяемое (строгое) распределение обязанностей между участниками какого-то бизнес-процесса по схеме Заказчик-Поставщик, то создание потребительского вытягивания – это создание системы сбора заказов.
Надо еще понимать, что потребительское вытягивание не существует в природе само по себе, к нему нельзя просто подключиться как к розетке, его нужно создавать, долго и упорно. Любая новая компания начинает с выталкивания, постепенно развивая систему вытягивания. Японцы так об этом и говорят, не можешь вытягивать, выталкивай. В самом выталкивании нет чего-то плохого, просто вытягивание гораздо эффективнее и надежнее выталкивания.
Кстати, осознание необходимости создания потребительского вытягивания, это самый большой вклад японцев в систему Деминга. Деминг обосновал необходимость создания системы внутреннего вытягивания, японцы пошли дальше.
Создание системы внешнего вытягивания – это, суть, главное отличие бережливого производства от «массового производства». Если при массовом производстве сначала производится товар, предположительно устраивающий покупателя, то при бережливом производстве производится только то, что действительно нужно покупателю, что подтверждается его заказом (и, соответственно, наличием реального платежеспособного спроса).
Запросы потребителя – это всегда очень подвижная цель, эти запросы постоянно меняются, и реагировать на эти изменения можно только имея систему прямого контакта с клиентами, систему сбора заказов. Сам заказ однозначно говорит о том, что нужно потребителю, компании не надо гадать, предполагать за потребителя, а просто качественно и в срок выполнять этот заказ. Понятно, что никто не мешает компании предлагать клиенту что-то новое, наоборот, только предлагая постоянно все большую и большую ценность клиентам, компания только и может процветать, но решение производить или не производить это новое (усовершенствованное) принимают сами клиенты, размещая или не размещая свои заказы. В Японии на этот счет есть понятие излишнего качества. Всегда можно сделать гораздо более сложный и, соответственно, более дорогой товар, но он может быть совершенно не нужен покупателю. Клиенту могут быть совершенно неинтересны его дополнительные функции или цена, которую ему приходится платить за эти дополнительные функции
Принцип создания «потока»
Смысл создания «потока» не в том, чтобы создать какой-то плавно движущийся конвейер или систему конвейеров, а в том, чтобы любой бизнес-процесс (и не только производственный) компании имел свой строгий замкнутый технологический цикл. Чтобы его можно было постоянно воспроизводить, совершенствовать, а любое отклонение от этого цикла сразу бросалось в глаза. Замкнутый цикл должен начинаться с одного и того же, проходить одни и те же стадии, и заканчиваться всегда одним и тем же. Нельзя начинать с середины процесса, перепрыгивать стадии, не доводить процесс до завершения, т.е. постоянно пытаться изобретать «хитрый» велосипед.
Замкнутый технологический цикл, «поток» – это единственная возможность совершенствования любого процесса. Чтобы что-то оценить, это сначала, надо измерить. Чтобы что-то усовершенствовать, это сначала надо строго описать. Систему, самую плохую, несовершенную, можно усовершенствовать, хаос усовершенствовать нельзя
Принцип постоянного совершенствования Кайдзен
Принцип постоянного совершенствования означает совершенствование всех бизнес-процессов компании. Совершенствование не вообще, хоть чего-то там, а именно совершенствования каждого бизнес-процесса. Деятельность любой компании состоит из нескольких функциональных процессов, каждый их которых состоит из своих технологических процессов, которые, в сою очередь, состоят из соответствующих подпроцессов и подподпроцессов. И постоянно совершенствоваться должны все эти бизнес-процессы.
При этом, надо иметь в виду, что целью совершенствования любого бизнес-процесса всегда является сокращение времени этого процесса за счет сокращения или исключения ненужных (не добавляющих ценности клиенту) операций, что автоматически приводит и к сокращению стоимости этого процесса
Принцип «Обеспечения качества с первого раза»
Принцип обеспечения качества с первого раза означает, что любая отдельная операция, из которой состоит процесс, должна быть выполнена очень тщательно. Тогда и конечный продукт этого процесса будет автоматически выполнен качественно. И наоборот, если хоть одна операция будет выполнена некачественно, то и конечный продукт процесса будет недостаточного качества.
Принцип «Обеспечения качества с первого раза» часто путают с принципом «Обеспечения качества за один проход» . Это совсем другой принцип. Этот принцип описывает получение высокого качества за счет комбинирования нескольких технологических операций в одной технологической линии. Если удается увязать несколько операций или весь технологический процесс в технологическую линию, а это возможно только при очень точном расчете и тонкой настройке (на порядок выше, чем при осуществлении отдельных операций) операций внутри технологической линии, то качество продукта этого процесса вырастает многократно
Принцип принятия решения «Немаваси»
Принцип принятия решения «Немаваси» преподносится, как поиск консенсуса между всеми сотрудниками, участвующими в том или ином процессе, при принятии руководителем этого процесса какого-то управленческого решения. На самом деле японский руководитель никогда не ищет консенсуса (согласия), это противоречит японским традициям. В Японии нет и не может быть двух равных человек. Один всегда будет руководителем (старшим), а второй подчиненным (младшим). Руководитель процесса не ищет согласия, он изучает все возможности решения проблемы, поэтому выслушивает каждого работника, участвующего в процессе, чтобы узнать мнение каждого о возможностях решения. Предложения каждого очень тщательно изучаются, но после того как руководитель выбрал лучший по его мнению вариант, он принимает решение, невзирая на согласие или несогласие тех, чьи предложения он проигнорировал. Правило выслушивать предложение каждого работника можно сравнить с нашим (советским и досоветским) способом использования «коллективного разума».
Член Совета директоров компании Тойота (имя, к сожалению, не помню) вспоминал, что когда он был молодым специалистом, ему пришлось работать в компании, которая занималась проектированием и строительством оросительной системы (системы каналов, дамб и шлюзов) рисовых полей. 70 лучших инженеров спроектировали эту систему и построили с использованием самых передовых достижений науки и техники. Система управлялась программой, и все было тип-топ. Но вскоре после запуска системы случились необычно продолжительные и обильные проливные дожди, и система не выдержала, что привело к ее остановке. При этом на соседних полях, где система орошения была построена 200 лет назад простыми крестьянами, продолжала работать в штатном режиме. Она управлялась в полуавтоматическом режиме, но работала как часы. Он стал изучать вопрос, а почему старая система справилась, а новая нет. И пришел к выводу, что 200 лет крестьяне работали «коллективным» умом, каждый вносил свои предложения, все их оценивали, испытывали и в результате останавливались на самом эффективном предложении. И это происходило не одни раз, а на протяжении всех 200 лет, система постоянно совершенствовалась. И этот накопленный опыт просто невозможно заменить интеллектом даже 70 самых лучших инженеров со всеми их новыми техническими возможностями
Принцип визуального контроля процесса Канбан
Принцип визуального контроля процесса самый извращенный на Западе принцип бережливого производства. В Инете можно увидеть множество роликов, где дяди и тети радостно подписывают разноцветные бумажки словами «готовится к работе», «поступило в работу», «находится в работе», «работа окончена» (или что-то в этом роде), прикалывают к стене, и объясняют непритязательной публике, что это японская система Канбан. Руководитель процесса, мол, сразу видит, какие процессы у него идут, и в какой они стадии находятся. Представить недотепу, который управляет процессом, но не видит (просто взглянув на процесс) в каком состоянии он находится, очень трудно. И трудно представить большей глупости, чем найм отдельного человека, чтобы он занимался откровенной ерундой, лишь бы руководитель не отвлекался от сна или другого приятного времяпрепровождения.
Это можно сравнить, как если бы тренеру по футболу приносили каждые 5 минут цветные бумажки со сведениями о том, куда рванули его нападающие или защитники, где они находятся и что там поделывают соперники. Тренер бы просил, а может вы мне просто покажете как идет матч, я сам все увижу, а ему отвечали, не стоит отвлекаться, пейте, закусывайте, перед большими гостями же неудобно. Канбан, мол, самая эффективная система визуального контроля.
Принцип визуального контроля потому и эффективен, потому что не требует дополнительных затрат и людей. Работник, когда у него возникла проблема (закончились комплектующие), просто поднял бумажный флажок, и те, кому следует, сразу это заметили и отреагировали. Или увидели сами, если сигнал возник автоматически, когда, например, от раскрашенной в красный цвет стены убрали последний экземпляр комплектующего. Человек, участвующий в процессе, в доли секунды обрабатывает такие сигналы, ему не нужны няньки. Кстати, на этой же способности человека все видеть и понимать без слов основан и другой принцип бережливого производства «Иди и смотри сам» (что-то вроде нашего «лучше один раз увидеть, чем сто раз услышать»)
Принцип «поставка точно в срок»
Этот принцип часто воспринимается как некое волшебство. Что в голову не пришло, тут же в течение 5 – 10 минут это что-то должно быть доставлено. Хотя это просто принцип точного планирования. Если производственный процесс требует поставки раз в день, 2 раза в день или один раз в час, то и поставки должны быть осуществлены в необходимом ритме. Не каждый поставщик может обеспечить необходимую компании ритмичность поставок, но в этом и заключается умение снабженцев. Надо найти если не прямых поставщиков, то компании (логистические центры, базы, склады), которые нужную ритмичность обеспечат. Да, у посредников цены будут чуть выше, но от неритмичности поставок (и, соответственно, производства продукции) убытки компании будут на порядок выше
Пресловутые 6 сигм
В свое время Деминг предложил шире использовать статистические методы контроля качества продукции. В настоящее время широкое распространение приобрел способ контроля на основе использования 6 сигм. При этом, этот способ контроля подается как способ совершенствования качества продукции. А это не так, контроль качества и совершенствование технологии производства – это не одно и то же.
Сигма – это среднеквадратическое отклонение. Оно потому и используется для контроля качества продукции, а точнее отдельных параметров продукции, что оно более точно, чем среднее арифметическое или взвешенное среднее арифметическое, отражает случайное отклонение какого-то параметра от заданной величины. И используют его не столько для контроля качества продукции, сколько для контроля качества, стабильности технологического процесса. Если параметры продукции, например, через каждые 1000, 10 тыс., 100 тыс., и т.д. единиц не отклоняются от заданных параметров на три сигмы в плюс или три сигмы в минус, то технология считается стабильной, гарантирующей заявленное качество продукции. И наоборот, если отклонения превышают ±3 сигмы, то технология считается нестабильной, не обеспечивающей заявленного качества, и требует восстановления (замены изношенных частей, заточки режущих поверхностей и пр.) или модернизации.
В заключение следует, видимо, отметить, что приведенными примерами не исчерпываются все проблемы, возникающие при внедрении бережливого производства (Lean Production), хотя основной проблемой все же является невнятное, смутное представление о системе бережливого производства
см. по теме:
Положение об организации бережливого производства (Lean production)
Бережливое производство (Lean Production) – система организации деятельности компании
Ключевые управленческие навыки руководителя
Здесь Вы можете задать вопрос. Это Вас ни к чему не обязывает, зато у Вас хоть одной неопределенностью, но станет меньше: