Бережливое производство
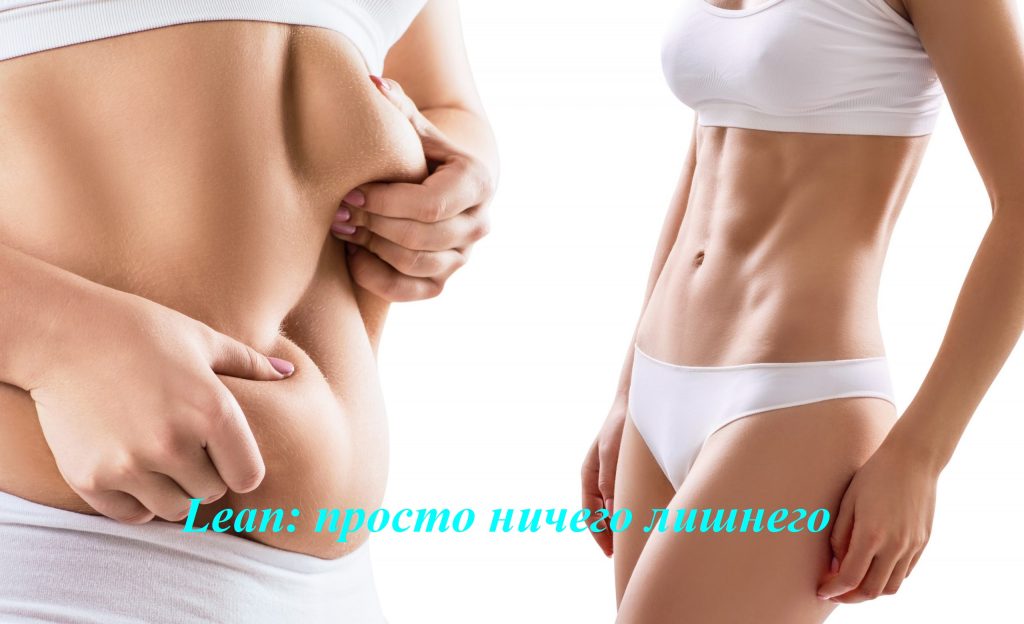
Бережливое производство (Lean Production) – это система организации деятельности компании, направленная на постоянное повышение качества продукции (товаров, услуг) компании за счет непрерывного сокращения ненужных (не добавляющих ценности) клиенту затрат ресурсов компании
Базовым принципом системы организации деятельности компании на принципах Бережливого производства является принцип, определяющий, что целью деятельности любой компании является постоянное повышение качества ее продукции (товаров, услуг), или другими словами, постоянное увеличение ценности, предоставляемой компанией потребителям своей продукции (см. Проблемы внедрения бережливого производства (Lean Production)).
Повышение качества продукции компании может (как при массовом производстве) достигаться механическим добавлением продукции дополнительных свойств за счет дополнительных операций и, соответственно, дополнительных затрат ресурсов. Что приводит к росту себестоимости такой продукции и ее цены. При бережливом производстве повышение качества продукции достигается за счет сокращения ненужных клиенту затрат времени, и, автоматически, ненужных клиенту затрат материальных ресурсов компании. Качество продукции компании растет (и, соответственно, цена этой продукции), а затраты на ее производство значительно снижаются. Lean Production потому, собственно, и бережливое, что качество достигается за счет исключения всего некачественного, временного, ненужного потребителю.
В условиях конкуренции (в условиях рыночной экономики) выигрывать борьбу за предпочтения покупателей можно только либо за счет повышения качества своей продукции, либо за счет снижения цены продукции. Бережливое производство позволяет компании развиваться одновременно в обоих направлениях, непрерывно повышать качество продукции за счет постоянного сокращения непроизводительных затрат (потерь). Понятно, что снижение затрат в этом случае не приводит к снижению и цены. Наоборот, постоянное снижение не добавляющих ценности затрат приводит к непрерывному повышению качества продукции и, соответственно, к повышению цены этой продукции
Содержание:
Повышение качества продукции на основе принципа Кайдзен
Сокращение потерь – способ реализации принципа Кайдзен
Перепроизводство
Время ожидания
Транспортировка
Лишние этапы обработки
Запасы
Ненужные перемещения
Выпуск дефектной продукции
Неиспользование творческого потенциала сотрудников
Потери от излишнего качества
Организация потока – способ выявления потерь
Повышение качества продукции на основе принципа Кайдзен
На первый взгляд, любое техническое усовершенствование продукции и, соответственно, технологии ее производства, может производится двумя путями: путем разработки новых технологических методов, или путем совершенствования уже используемых технологических методов. На самом деле, любые новые технологические методы – это старые методы, которые подверглись изменению, слиянию, замене или применению известных, но ранее не использованных методов. Абсолютно новые технологические методы появляются довольно редко, это связано напрямую с научными открытиями. Такие открытия случаются довольно редко, а с момента открытия до получения способов применения этих новых знаний на практике проходит еще довольно большой срок. В таких случаях происходит массовое перевооружение всей промышленности. В период от одного массового перевооружения промышленности до другого единственным путем совершенствования качества продукции компании является совершенствование используемых или новое применение уже известных технологий. И целью такого совершенствования является сокращение времени всех технологических операций (повышение производительности труда) компании, что автоматически приводит к сокращению и материальных затрат компании.
Сокращение потерь (ненужных затрат) автоматически приводит к совершенствованию качества продукции компании. Качество операций, точность обработки растет, а это приводит к улучшению практически всех параметров продукции. При этом, автоматически исключаются и излишние (бессмысленные) затраты материальных ресурсов.
Если технологически возможно получить необходимое качество продукта (комплектующего, товара, услуги), используя меньшее количество материала (а на обработку большего количества материалов требуется и большее количество времени) и рабочего времени, то просто глупо тратить на это впустую (в ущерб) излишнее количество материала и времени.
Это можно показать на следующем примере. Все знают, что японские инструменты все еще качественнее российских. При этом, если спросить у пользователей, а чем именно они лучше, то ответы будут примерно такими, более простые в работе, более надежные, более легкие, более производительные. Да, наши инструменты по отдельным параметрам могут быть не хуже и даже превосходить японские, но зато по всем другим значительно проигрывать. За счет этого общее качество оценивается потребителем продукции как недостаточное.
Особенно часто профессионалы указывают на более малый вес японского инструмента. И это неспроста. Еще наш инженер, Василий Гаврилович Грабин, занимавшийся до и во время ВОВ, разработкой пушек, привлекал к разработке специалистов по физиологии человеческого тела, чтобы создавать орудия, при обслуживании которых в бою боец меньше бы уставал. Еще и слова такого не было, как эргономика, а наш инженер уже тогда понимал, что экономия физических сил работника (бойца), это очень важный фактор эффективной работы. Как только человек устает, он начинает совершать множество ошибок, а это недопустимо. Чтобы сократить количество возможных ошибок, надо добиваться того, чтобы работник уставал как можно меньше, другими словами, добиваться экономии труда. Потому профессионалы, которым приходится работать инструментом по многу часов подряд, и выбирают более легкий (хотя и боле дорогой) японский инструмент.
Понятно, что совершенствование продукции и соответствующей технологии ее производства не ограничивается только эргономичностью. Все другие параметры продукции и соответствующих технологических процессов подлежат постоянному совершенствованию.
В системе организации деятельности компании на принципах Бережливого производства (Lean Producion) постоянное повышение качества продукции компании осуществляется за счет непрерывного совершенствования бизнес-процессов компании, из которых, собственно, и состоит ее деятельность. В бережливом производстве процесс совершенствования бизнес-процессов описывается принципом постоянного совершенствования Кайдзен
Сокращение потерь – способ реализации принципа Кайдзен
Любой процесс состоит из определенной последовательности операций, которые могут выполняться последовательно друг за другом или параллельно. При этом, любой процесс, даже самый высокоорганизованный, не является идеальным, он обязательно включает какие-то этапы, какие-то операции, которые не добавляют стоимости продукту, не являются производительными. В бережливом производстве принято выделять следующие виды непроизводительных операций (потерь)
Перепроизводство
Потери от перепроизводства возникают, когда компания производит больше продукции, чем нужно потребителям (рынку). Стараясь сэкономить на объеме, на сокращении затрат на единицу продукции, компания производит максимально возможное количество продукции. По сути, она работает на склад, рассчитывая в дальнейшем как-то растолкать эту продукцию среди покупателей. На практике это приводит к затовариванию, к необходимости содержания складских мощностей и складского персонала. В конечном итоге это приводит к необходимости снижать цены, чтобы хоть как-то суметь продать весь этот объем продукции. Предполагаемая экономия на объеме оборачивается прямыми убытками, которые могут значительно превышать предполагаемую экономию.
Для исключения потерь от перепроизводства при бережливом производстве компания производит ровно столько продукции, сколько было заказано клиентами. Это описывается в бережливом производстве принципом «Организации вытягивания». Компания не работает на склад, не содержит складские помещения, не содержит ненужный персонал, все что производится сразу отправляется заказчику. И не производится ничего, что не подтверждено платежеспособным спросом, заказом клиента.
Стоит отметить, в постсоветской экономике в низкоконкурентных отраслях компании могли гнаться за объемом и продавать почти любое количество дефицитной продукции, не теряя в цене, но в условиях высококонкурентной среды, когда весь рынок уже поделен, к потребителю можно пробиться (увеличить свою долю рынка) только либо за счет опережающего конкурентов качества своей продукции, либо за счет более низкой цены. Экономия на объеме уже потеряла смысл. Если производить больше, но не совершенствовать качество продукции, придется резко снижать цены, чтобы все распродать. И это приводит не к увеличению своей доли рынка, а к постепенному, но неуклонному, снижению этой доли.
В свое время Деминг (идеолог бережливого производства) предложил создание системы внутреннего вытягивания, когда каждый следующий в цепочке (последовательности технологических операций) операций работник, является Заказчиком для работника предыдущей операции, а работник предыдущей операции, соответственно, является Поставщиком для работника следующей операции. Японцы довели эту систему до совершенства. В цепочке связей Заказчик-Поставщик работник самой последней операции является конечным Заказчиком всего процесса, и все другие работники подчинены его требованиям (заказам). Конечный Заказчик требует предоставления необходимых ему для конечной сборки деталей, а его поставщики требуют уже от своих поставщиков (и так вниз по цепочке) детали или комплектующие, необходимые им для выполнения требования (заказа) своего Заказчика. Работники, участвующие в процессе, выполняют операции не в произвольном порядке и не в произвольное время, а выполняют их только тогда, когда они видят (чрез систему визуального контроля Канбан), что их Заказчику по процессу необходимы производимые этим работником комплектующие. Если работник видит, что его Заказчику его комплектующие в данный момент не нужны, то он останавливает свою работу до тех пор, пока Заказчик не сообщит о вновь возникшей у него потребности. Так работает внутреннее вытягивание. Это еще один способ борьбы с потерями от перепроизводства. Не только конечная продукция компании не производится впрок, но и все промежуточные продукты (полуфабрикаты) производятся только тогда, когда они кому-то нужны, когда на их производство есть заказ.
Любой процесс организуется по принципу «Равномерного распределения нагрузки Хэйдзунка» (работай как черепаха, а не как заяц), работа осуществляется без спешки (в соответствии с принципом «Обеспечения качества с первого раза», не путать с принципом «Обеспечения качества за один проход»), при этом каждая отдельная операция выполняется очень тщательно. Многие, наверное, обращали внимание, как работают в роликах на Ютуб японские столяры, нам кажется, что очень уж медленно. Зато они практически никогда не производят брака и не переделывают испорченную деталь. Японцы так работают при осуществлении любых производственных (и непроизводственных) операций. Поспешишь, людей насмешишь. При этом любой процесс отрегулирован таким образом, что в нем практически не бывает простоев или авралов. Авралы, как известно, это причина всех ошибок, причем самых нелепых ошибок
Время ожидания
Любой процесс состоит из отдельных операций, которые при их последовательном выполнении, задерживают выполнение следующих операций. Для сокращения времени ожидания используется принцип «Обеспечения качества за один проход». Он подразумевает организацию параллельного выполнения операций за счет создания комбинированных систем обработки, технологических линий
Транспортировка
При выполнении каких-то операций с материальными ресурсами возникает естественная потребность их транспортировки с места на место. Для устранения этих потерь также используется принцип «Обеспечения качества за один проход», создание комбинированных систем обработки, технологических линий, которые включают в себя и автоматическую транспортировку материальных ресурсов в течение всего технологического процесса. Понятно, что для этих целей лучше всего подходит конвейер (система конвейеров)
Лишние этапы обработки
Для обработки какого-то материала могут использоваться различные операции, например, резка, грубая абразивная обработка, тонкая шлифовка. Для получения необходимого качества обработки можно использовать более точную резку, которая устранит необходимость в грубой абразивной обработке. Деталь или комплектующее после обрезки можно сразу подвергать тонкой шлифовке. Для сокращения лишних этапов обработки можно также применять комбинированные методы обработки, когда одновременно производится две или более операции, резка и шлифовка, например, или технологические линии, объединяющие множество операций, некоторые из которых вполне можно исключить при автоматизации соответствующего процесса.
Чтобы создать технологическую линию (реализовать на практике принцип «Обеспечения качества за один проход»), которая в автоматическом режиме производит несколько операций (которые до этого выполнялись по отдельности), требуется приложить немало усилий, чтобы увязать все эти операции, снабдить их автоматической подачей (транспортировкой) и автоматическими системами контроля качества. Это требует очень точного расчета всех операций, точного расчета всех перемещений и очень тонкой настройки системы. И если этого удается добиться, то качество выполнения операций, объединенных в эту систему, возрастает многократно. Что, в свою очередь, значительно повышает и качество конечной продукции компании
Запасы
В бережливом производстве запасы рассматриваются как один из основных источников убытков компании. Поэтому компания приобретает ровно столько материальных ресурсов, сколько ей нужно для выполнения заказов своих клиентов. При чем, определяется дневная или даже часовая потребность в этих ресурсах. Такая практика описывается принципом «Поставка точно в срок». Считается правильным, когда утром перед началом работы необходимые материальные ресурсы поступают, а к концу рабочего дня не должно ничего оставаться. Причем материальные ресурсы поступают не на склад, а складируются прямо в цеху в местах, максимально приближенных к местам выполнения тех технологических операций, в которых используются эти ресурсы. Приобретение материальных ресурсов сверх необходимого объема, рассматривается в бережливом производстве как заведомые потери. Запасы материальных ресурсов надо охранять, создавать необходимые условия хранения, содержать дополнительный персонал, к тому же, эти ресурсы могут банально разворовать, в том числе и собственные сотрудники. Для устранения таких потерь и используется строгая ритмичность поставок. Такая ритмичность поставок обеспечивается особыми отношениями компании со своими поставщиками. Эти отношения описывается принципом «Уважай своих поставщиков, ставь перед ними сложные задачи». Нам даже трудно сразу понять этот принцип. Для нас уважать – это значит, делать поблажки, снижать требования, облегчать задачи. Мы даже не задумываемся, что это приводит к деградации того, кому мы делаем поблажки, облегчаем жизнь. У нас любой добившийся успеха в жизни человек из низов считает своим долгом максимально облегчить жизнь своим детям, сделать их максимально не приспособленными к жизни. Японцы же наоборот, считают, для того чтобы люди не деградировали (а развивались), им нужно задавать все более и более сложные задачи. Так, например, дети императора должны получать гораздо более сложные задания, чем любые другие дети. Если ребенок в обычной школе должен выучить стихотворение размером в половину страницы, то сын императора должен выучить стихотворение размером в 5 страниц. Сын императора не должен быть неженкой, слабаком, а, наоборот, он должен быть самым сильным, выносливым, терпеливым. И так во всем. Если любишь или уважаешь человека, ставь перед ним сложные задачи, помогай ему совершенствоваться, расти, помогай ему стать сильнее.
Если поставщики готовы к постоянному совершенствованию свой деятельности, готовы подстраиваться под запросы покупателя и выдерживать необходимый компании ритм поставок и качество поставляемых ресурсов, то только с такими поставщиками и заключаются долгосрочные договора. Понятно, что поставщики, не желающие работать над совершенствованием своей деятельности и подстраиваться под запросы клиента, очень быстро теряют клиентов и вылетают с рынка.
Здесь еще стоит заметить, что японцы очень серьезно восприняли призыв Деминга «покончить с практикой закупок по самой низкой цене». Надо ориентироваться не на цену покупки материальных ресурсов, а на их эффективную стоимость. Сырье можно купить, например, стоимостью 30 тыс. рублей за тонну, но с выходом из этого сырья готовой продукции в размере 60%, а можно купить сырье по цене 35 тыс. рублей за тонну, но с выходом готовой продукции – 75%. В результате получится, что якобы дешевое сырье реально стоит 50 тыс. рублей за тонну, а якобы дорогое – 47 тыс. рублей. И это не считая еще затрат труда, энергии, амортизации ОС и материалов на переработку отходной части объема сырья. Эффективная стоимость «дешевого» сырья может легко дойти уже до 70-80 тыс. рублей за тонну.
Или в случае с приобретением материальных ресурсов у посредников с наценкой, например, 10 % от цены завода-изготовителя. На первый взгляд кажется, что глупо переплачивать посреднику 10%, но это только на первый взгляд. Если начать считать, то окажется, что содержание штата снабженцев, складских помещений и оборудования, складского персонала, автотранспорта, ГСМ обходится компании в год гораздо дороже, чем наценка в 10 % от стоимости закупаемых ресурсов. Это можно показать на следующем примере.
Компания закупает, например, сырье у завода-производителя по цене 30 тыс. рублей за тонну и сама вывозит это сырье своим автотранспортом мелкими партиями по 3 тонны за рейс. В месяц она делает, например, 15 рейсов. Стоимость приобретенного сырья за месяц составит 1 350 тыс. рублей (3*15*30). Она может тот же объем закупить у посредника, который будет доставлять это сырье с той же ритмичностью на производственную площадку компании по цене 33 тыс. рублей за тонну (с наценкой 10%). Общая стоимость сырья за месяц составит 1 485 тыс. рублей (3*15*33), на 135 тыс. рублей дороже. Но компания затратит гораздо больше на ГСМ, на зарплату водителя, зарплату экспедитора, если сама будет заниматься доставкой этого сырья (500км – 40л/100км=200л) (15рейсов*200л*45 руб. = 135 тыс. руб.) (2чел*35тыс. руб.*1,3страх.взн. = 91 тыс. руб.), 135 тыс. руб. + 91 тыс. руб. = 226 тыс. руб. Если начать считать реальные затраты, то становится очевидным, что осуществлять закупки нужно исходя именно из расчета эффективной стоимости закупок, а не по самой дешевой цене
Ненужные перемещения
В отличие от транспортировки перемещения представляют собой переворачивания предметов, их последовательное отодвигание или приближение, например, к режущему станку, и тому подобные манипуляции. Для сокращения или устранения потерь от таких операций используют все тот же принцип «Обеспечения качества за один проход», ищут способы комбинированной обработки предмета труда (детали, комплектующего), или способы, облегчающие такие манипуляции (подвешивание предмета или подвешивание обрабатывающих инструментов)
Выпуск дефектной продукции
В бережливом производстве брак рассматривается как прямые убытки. На изделие уже были потрачены материалы, энергия и рабочее время. Для его переделки (что очень затруднительно) необходимо затратить даже больше ресурсов, чем на его производство. Обычно проще просто сдать на металлолом и списать затраты на убытки. Для устранения таких потерь используют встраивание в технологический процесс системы контроля качества и остановки процесса в случае выявления несоответствия качества обрабатываемого предмета необходимому, а также системы защиты от ошибок (защита от дурака), когда процесс автоматически останавливается, если выполнено недопустимое действие. Создание таких систем описываются, соответственно, принципами «Дзидока» и «Пока-ёкэ» («Бата-ёкэ»).
В качестве примера встраивания в процесс системы контроля и остановки процесса можно привести ставший уже хрестоматийным пример Сакити Тоёда (отца основателя Тойота Мотрс Киитиро Тойёда), вернее его автоматический ткацкий станок, который включал в себя устройство остановки работы станка, когда обрывалась хоть одна нить. Если раньше при обрыве нити станок продолжал работать, производя иногда километры бракованной ткани, то оборудованный новым механизмом остановки, он предотвращал производство бракованной продукции. Кстати, именно на вырученные от продажи англичанам патента на этот станок деньги, его сын Киитиро Тойёда и основал компанию Тойота Моторс. Понятно, что с момента основания Тойота Моторс, все ее производственные процессы оснащались механизмами остановки процесса («Дзидока») в случае выявления причин, приводящих к производству брака или недостаточно качественной продукции.
В качестве примера «Защиты от дурака» можно привести пример японских автомобилей, оборудованных алко-замком или системой издания звуковых сигналов при незакрытой двери автомобиля
Неиспользование творческого потенциала сотрудников
Этот вид потерь был сформулирован американским исследователем бережливого производства Дж. Лайкером. Тайити Оно, руководитель компании Тойота, который сформулировал приведенные выше виды потерь, не стал выделять этот вид потерь в отдельный вид. Для японского менталитета использование творческого потенциала (коллективного разума) всех сотрудников, участвующих в процессе, является само собой разумеющимся. Это описано принципом принятия решений на основе изучения мнений всех членов процесса «Немаваси». Для людей и народов, производственной и управленческой культурой которых не предусмотрено изучение руководителем какого-либо процесса мнений всех без исключения сотрудников, участвующих в этом процессе, этот вид потерь является наиболее важным.
Во всем мире принято считать, что усовершенствованием технологических процессов должны заниматься специально обученные люди, инженерно-технический персонал, а рядовые исполнители, сотрудники рабочих специальностей, не могут ничего совершенствовать. Да, поиск технических способов совершенствования процессов, это действительно прерогатива ИТР, но в вопросах практического совершенствования отдельных операций, из которых и состоит любой процесс, такие сотрудники ничего не могут предложить. Это практически недоступно вниманию и пониманию ИТР. Они этого просто не видят, процесс целиком видят, этапы этого процесса видят, а миллионы деталей, тонкостей этого процесса остаются для них невидимыми, это естественно. Зато сотрудники, выполняющие отдельные операции, прекрасно знают свои операции и видят множество способов их совершенствования. Если их никто не спрашивает о том, что они могут предложить по совершенствованию их операции (операций), то эти операции годами и десятилетиями остаются вне процесса усовершенствования. Работники думают, что так и должно быть. Зачем что-то совершенствовать, если это никому не нужно.
Такой подход к совершенствованию процессов и является основным отличием массового производства от бережливого производства. В Японии процесс совершенствования процесса начинается снизу. Из десятков, сотен и тысяч усовершенствований, предлагаемых рядовыми сотрудниками, и складывается процесс постоянного совершенствования Кайдзен. Понятно, что инженерно-технический персонал тоже ищет технические способы совершенствования процесса, но на базе предложений сотрудников, непосредственно осуществляющих отдельные операции этого процесса. Технические специалисты не рассуждают как-то вообще, не витают в облаках, а осмысливают, как можно технически осуществить предложения непосредственных исполнителей. Предложения непосредственных исполнителей составляют настолько огромный потенциал инноваций, что неиспользование этого потенциала это уже не просто потери, это смертный грех
Потери от излишнего качества
Этот вид затрат японцы не выделяют отдельно как потери, но пользуются принципом «Недопустимости излишнего качества». Для правильного понимания бережливого производства этот вид потерь очень важен, особенно для постсоветских стран. Потери от излишнего качества – это затраты на придание продукции либо бессмысленной сверхнадежности («солидной» монументальности), либо дополнительных свойств, не нужных потребителю.
Это можно показать на примере сравнения советского магнитофона и японского (времен СССР). Если в нашем магнитофоне все части были металлическими, то начинка японского магнитофона на 70-80 % состояла из пластиковых деталей. Это объяснялось не стремлением японцев к миниатюризации, а здравым смыслом. Если для протяжки магнитной ленты в принципе требовалась очень маленькая мощность электродвигателей, то зачем нужны мощные электродвигатели, которые будут крутить все эти мощные металлические шестерни. Пластиковые шестерни легко могут справиться с передачей небольшой нагрузки, необходимой для протяжки ленты. В результате японский магнитофон имел маломощные, но вполне достаточные для протяжки ленты электродвигатели, и пластиковые шестерни, которые эффективно и надежно передавали эту небольшую нагрузку. Что, в свою очередь, очень позитивно сказывалось и на чистоте звучания. Он практически не шумел.
В качестве примера добавления продукции ненужных потребителю свойств достаточно привести китайский калькулятор с музыкой. Примитивный, тяжелый, с большими батарейками, зато с музыкальным сопровождением любого нажатия на клавиши
Организация потока – способ выявления потерь
В системе организации деятельности компании на принципах бережливого производства (Lean Production) основным инструментом совершенствования бизнес-процессов компании является создание «Потоков», замкнутых технологических циклов этих процессов. Для того, чтобы получить возможность устранять потери, об этих потерях сначала надо еще узнать. Создание «Потока» – это как раз способ выявления потерь. Когда процесс строго описан (стандартизирован), т.е. представлен в виде строгой последовательности технологических операций, сразу становятся видны все его нестыковки, шероховатости, малоценные или совсем ненужные операции и, соответственно, потери. Это очень мощный инструмент совершенствования процесса. Все сводится к поиску возможностей сокращения или исключения потерь, т.е. к поиску возможностей совершенствования отдельных операций (или этапов) процесса и, соответственно, всего процесса.
Именно исходя из необходимости создания «Потока», создания и стандартизации замкнутого технологического цикла, компания Тойота внесла изменения в предложенную Демингом схему непрерывного совершенствования бизнес-процессов: PDCA (Plan – Do – Check – Act – планируй-действуй-оценивай-корректируй). Компания Тойота заменила первую стадию цикла Деминга на «Стандартизируй». Цикл совершенствования бизнес-процессов компании Тойота имеет вид: SDCA (Standardise – Do – Check – Act – стандартизируй-действуй-оценивай-корректируй). Понятно, что цикл совершенствования бизнес-процессов японцы для себя формулируют еще точнее: Стандартизируй процесс (создавай поток) – Выполняй работу в соответствии со стандартом – Оценивай результаты работы (ищи возможности устранения потерь) – Вноси изменения в стандарт (совершенствуй поток за счет устранения потерь).
Здесь нужно упомянуть очень важный принцип, который формально не считается принципом бережливого производства, но имеет к его пониманию самое прямое отношение. Принцип «Найди лучшее в мире, и сделай (это лучшее) еще лучше!» стал девизом восстановления и модернизации японской экономики после Второй мировой войны. Кстати, в это же самое время происходило внедрение в практику и бережливого производства. Японцы не пытались изобретать велосипед, они просто копировали лучшие мировые образцы и путем совершенствования своих бизнес-процессов делали свою аналогичную продукцию гораздо лучше заимствованных образцов. Японцы всегда были слабы в разработках, зато они очень сильны в усовершенствованиях. На новые разработки нужны ресурсы, квалифицированные специалисты, время, а после войны всего этого у них не было. Зато они получили возможность учиться и нещадно копировать (законно уворовывать) чужие разработки у американцев и европейцев. Кстати, советский опыт и разработки они тоже очень активно копировали.
В журнале «Изобретатель и рационализатор» за 1987 (или 1988г, но не суть) была опубликована статья о том, как наш инженер, специалист по штамповке, обучал японцев штамповке деталей кузова автомобиля из листового металла. Японцы закупили у американцев самое передовое оборудование, но не могли на нем ничего произвести. Как бы не пытались, получался один брак. Наш инженер немного их помурыжил, ему самому хотелось больше узнать об их промышленных приемах, потом на пальцах быстро все объяснил. Одним нажатием пресса нельзя сразу получить готовую деталь. Металл просто будет рваться в местах наибольших сгибов, в местах приложения наибольшей нагрузки. Сначала нужно произвести несколько слабых нажатий в местах предполагаемых сгибов, чтобы появились как-бы дорожки, по которым металл пойдет при штамповке, а только потом подготовленную поверхность подвергать окончательной штамповке. Это как грызть кедровые орехи, чтобы при раскусывании скорлупы ореха ядро не раскусывалось на половинки. Сначала надо несильно надкусить орех в его середине пару раз как бы с 4-х сторон, а только потом в месте ребра слабых надкусов чуть сильнее надкусить. Скорлупа расколется именно по линии слабых надкусов, а ядро останется целым. Сибиряки поймут.
Если пытаться совершенствовать допотопную технологию, как часто пытаются у нас с помощью бережливого производства совершенствовать давно устаревшие технологии, то толку от этого не будет. Использовать и совершенствовать имеет смысл только передовые технологии. Если какую-то технологию не получается разработать самому (при всем нашем большом таланте к разработкам), то ее следует позаимствовать у других, и сделать ее еще лучше. Это гораздо быстрее и эффективнее. Тем более, что ничто не мешает при совершенствовании чужой передовой технологии использовать и свои собственные разработки.
Это как получилось с производством композитного крыла для лайнера МС-21. Американцы и японцы отказались нам продавать свои линии по производству элементов фюзеляжа и крыльев из композитных материалов. Пришлось покупать у немцев. Их оборудование было чуть хуже американского и японского, но наши спецы легко его модернизировали, а уж в разработках композитных материалов нам в мире нет равных. В результате получили современную передовую технологическую линию, и стали производить элементы фюзеляжа и крылья, которые по своему качеству опережают всех конкурентов, а по цене опережают их в несколько раз. И сегодня МС-21 летает на нашем композитном крыле. А если бы стали пытаться все делать сами, получили бы сегодняшние результаты лет через 5 – 10.
В заключение следует отметить, что постоянному совершенствованию подлежат не только производственные процессы, а и все другие функциональные бизнес-процессы компании. И маркетинг, и бухгалтерский учет, и реклама и пр., имеют свои «потоки», свои потери, и возможности совершенствования «потока». Бережливое производство (Lean Production) – это система организации всех бизнес-процессов компании, организации всех функциональных видов ее деятельности
см по теме:
Положение об организации бережливого производства (Lean production)
Проблемы внедрения бережливого производства (Lean Production)
Здесь Вы можете задать вопрос. Это Вас ни к чему не обязывает, зато у Вас хоть одной неопределенностью, но станет меньше: